不知道大家有沒有發(fā)現(xiàn)一個現(xiàn)象,最近幾年新車更新?lián)Q代的速度越來越快了。像大眾這樣的傳統(tǒng)國際大廠,從立項到量產(chǎn)一款新車通常需要54個月的時間,國內(nèi)的傳統(tǒng)車企基本也在36個月左右??涩F(xiàn)在的新勢力車企已經(jīng)將研發(fā)測試周期縮短到了24個月,甚至有傳聞某些車企已經(jīng)縮短到15個月以內(nèi)了,速度堪比手機。這些變化也給大家?guī)砹艘恍┮苫蠛蛽鷳n,新車開發(fā)周期一而再、再而三地縮短,這背后是技術(shù)進步的結(jié)果,還是車企為了短期銷量和利潤,忽視了產(chǎn)品性能呢?

在介紹新車研發(fā)時間縮短的原因之前,我們有必要先大致了解一下新車的研發(fā)流程。按照主流車企的開發(fā)標準,新車研發(fā)流程分為方案、設計/驗證、投產(chǎn)三個主要階段。其中方案階段耗時9.5個月、設計/驗證14個月、投產(chǎn)10.5個月,最后加上2個月的上市階段,一共就是36個月。不難看出,新車開發(fā)中設計/驗證的耗時最長,縮短開發(fā)周期自然也要從它入手。


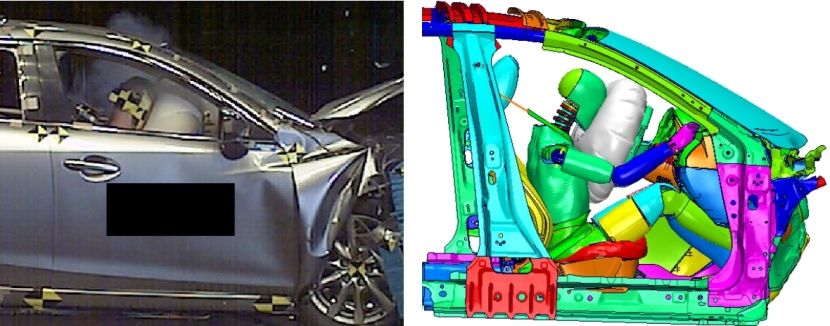
如何才能有效地縮短設計/驗證的時間呢?各家車企在這一點上基本都達成了一致,那就是采用CAE仿真技術(shù)。簡單來說,CAE就是把車輛基本信息錄入仿真軟件,通過軟件來模擬計算,然后再比較不同設計方案的優(yōu)劣勢。千萬別小看CAE技術(shù),它能夠模擬的領(lǐng)域非常多,比如車身碰撞安全性、氣動性能、NVH等等。也就是說,現(xiàn)在開發(fā)新車,前期幾乎不需要把設計圖紙轉(zhuǎn)換為真實零件,然后挨個去做物理測試,而是只用在電腦上敲擊鍵盤鼠標,各種零件的特性就一目了然了。
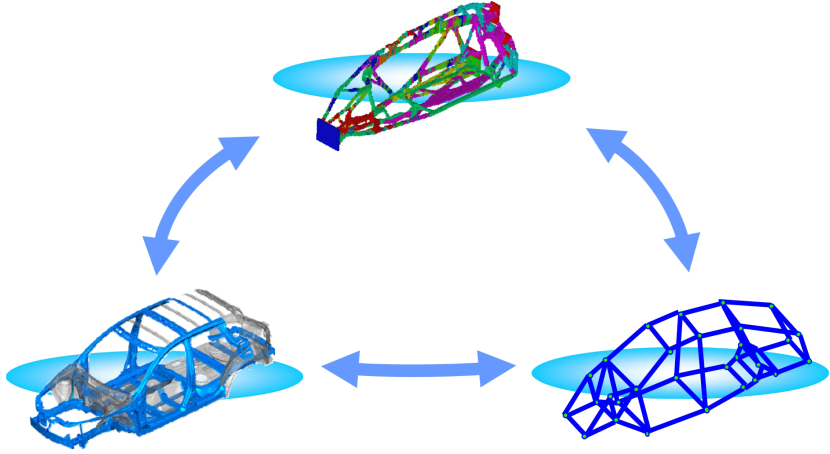
這么說可能還是有點籠統(tǒng),下面我們就說一些實際的案例。馬自達在開發(fā)第一代CX-5的車身時,理論方向很明確,那就是車身的傳力路徑不要彎曲,應該盡量設計成筆直的直線,另外車身的傳力路徑要多,而且傳力路徑要連貫。
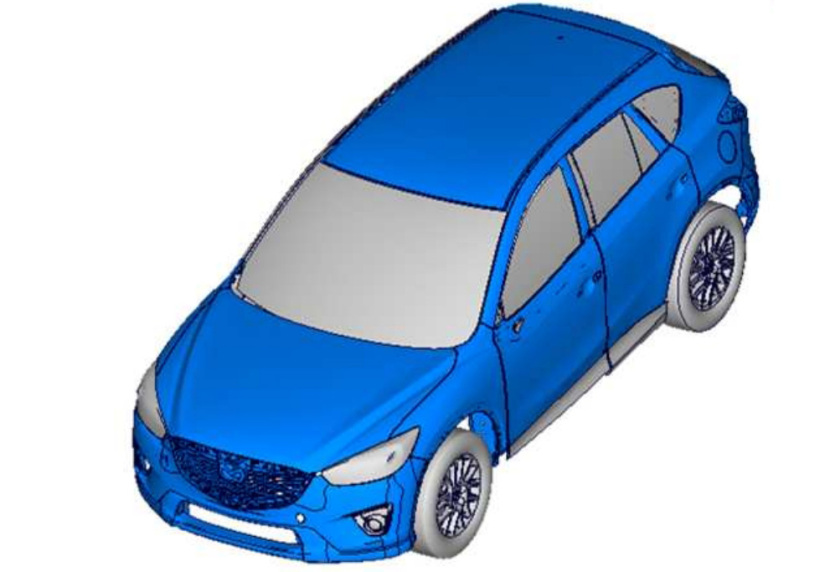
但是具體到縱梁與車身是斜著布置還是垂直布置,哪一種設計安全性更好時,還是要經(jīng)過大量的測試和驗證,所以馬自達就用到了LS-DYNA這款軟件分析車身的碰撞性能。簡單來說,馬自達首先將CX-5的尺寸、結(jié)構(gòu)做成一個CAD模型,然后把車輛的CAD模型導入LS-DYNA這款軟件,緊接著將車身不同部位的材料數(shù)據(jù)輸入進去。
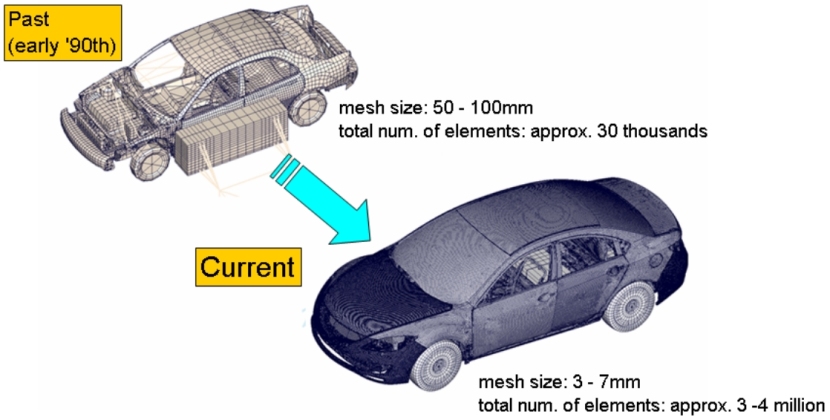
為了精確分析車身碰撞時局部的變形和潰縮,在LS-DYNA中還需要把車身分成細小的網(wǎng)格,一般網(wǎng)格越小仿真越接近真實情況。像90年代馬自達的車身仿真,網(wǎng)格的尺寸在50-100mm,因此整個車身被分為3萬個網(wǎng)格。而近些年馬自達的車身網(wǎng)格尺寸已經(jīng)縮小到了3-7mm,車身一共由300-400萬個網(wǎng)格組成。當然,網(wǎng)格數(shù)量越多計算時間越長,因此車企想要獲得更好的仿真效果,就需要有更強的計算能力,這也是為什么現(xiàn)在有些車企一直在強調(diào)自建超算中心的原因。
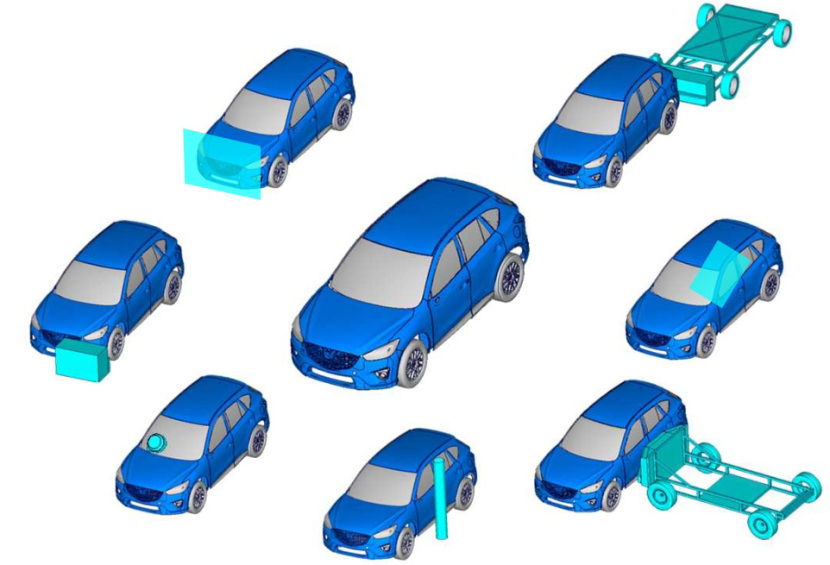
當以上步驟完成后,就只用在LS-DYNA中設定你想要的測試場景,比如偏置碰撞、側(cè)碰、速度等等,然后通過仿真計算就可以看到不同方案的區(qū)別。
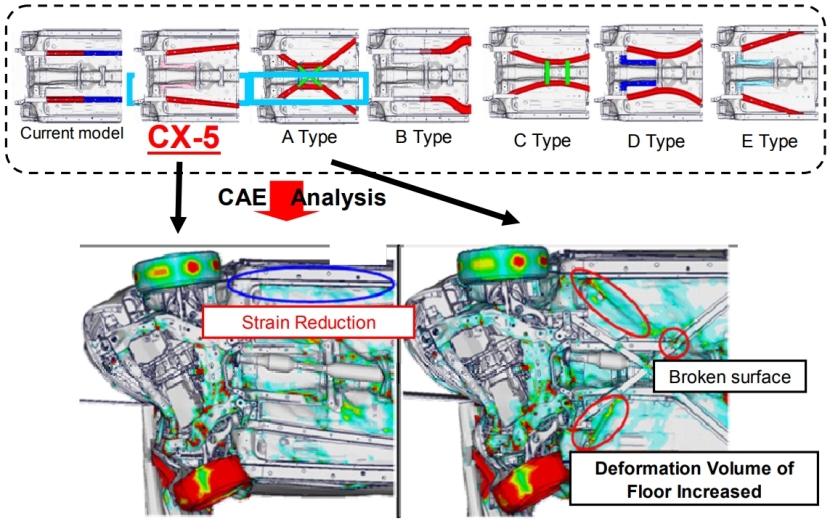
例如在設計CX-5底盤的縱梁時,馬自達對比了7種方案,最后從計算的結(jié)果可以看到,縱梁微微傾斜呈V字形時,在偏置碰撞中門檻梁變形幅度最小,而X形的縱梁應力過于集中有變形的風險,因此量產(chǎn)車型最終選擇了V字形方案。
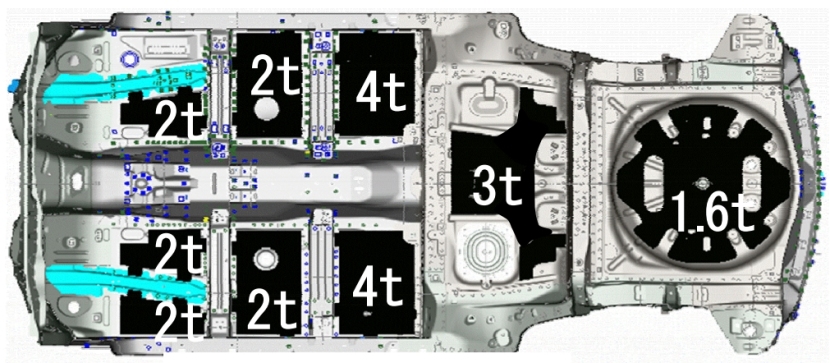
除了碰撞安全性之外,像是車身的NVH性能也經(jīng)常用到CAE仿真,只不過所使用的軟件不一樣。比如在分析車身中高頻噪音,以及如何布置車身的吸音、隔音、阻尼材料時,各大車企經(jīng)常會用到VA One等軟件。還是以CX-5為例,在車內(nèi)地板使用阻尼材料時,如果整個地板都使用同樣厚度的阻尼材料,那么車身重量就會提高,而隔音性能并不會因此變好。
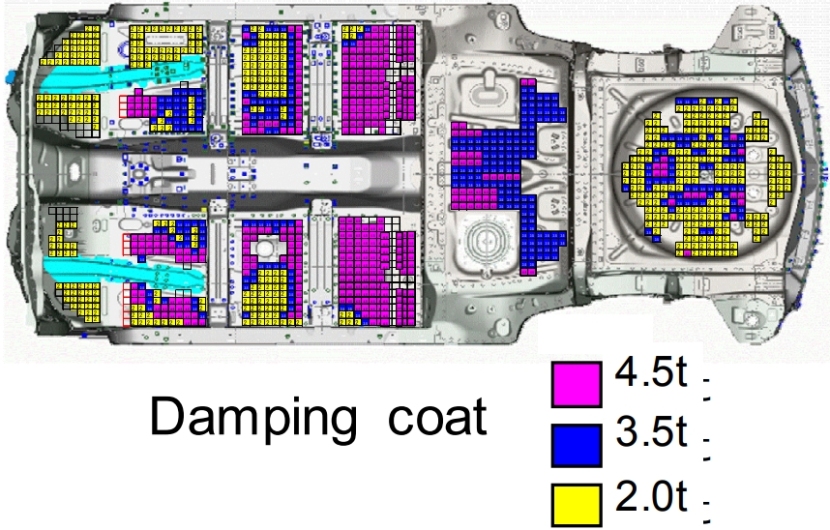
但是將CX-5的車身信息導入到NVH分析軟件后,就可以直觀的看到底盤每個部位噪音、震動的大小差異,然后根據(jù)震動大小來鋪設阻尼材料。像CX-5的后排地板部位,它的噪音、震動就比較大,所以需要使用厚一點的阻尼材料,而備胎槽只有一小塊區(qū)域噪音震動較大,其余比較小,所以可以用薄厚兩種材料搭配使用。由于使用了先進的CAE仿真技術(shù),CX-5在隔音性能不變的情況下,車身地板阻尼材料重量反而降低了2.4kg。
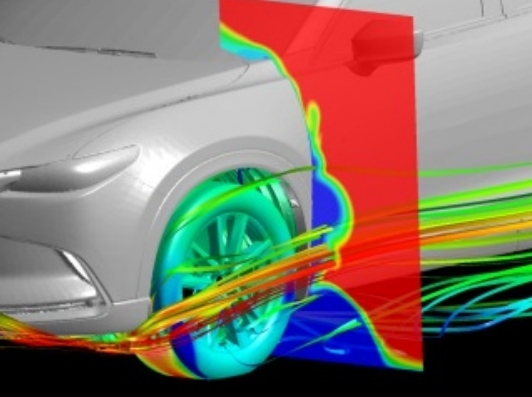
在氣動性能方面,CAE也是必不可少的環(huán)節(jié),同前面一樣把車輛的CAD模型導入STAR-CD等氣動性能仿真軟件內(nèi),然后設定測試條件,那么車身整體或局部的風阻、空氣流向、車身表面壓力等信息就可以完整的展現(xiàn)出來。而且根據(jù)馬自達提供的數(shù)據(jù),氣動性能仿真與風洞測試的風阻誤差可以控制在3%以內(nèi)。
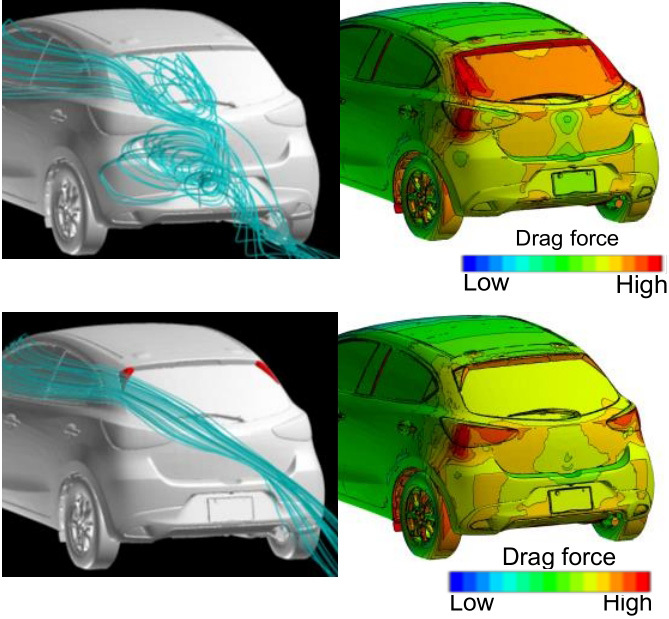
因為仿真的精度和還原能力非常高,所以通過氣動仿真軟件,車企可以針對車身的局部細節(jié)進行打磨從而一點點地降低風阻。比如在馬自達CX-3上,通過仿真計算發(fā)現(xiàn),當氣流通過前傾的后風擋玻璃與C柱時會產(chǎn)生巨大的渦流,從而導致風阻提升。但如果在后風擋與C柱上側(cè)夾角的位置增加一個擾流板,渦流就會大幅減少,整車風阻因此降低了1%。
其實,CAE仿真在汽車上應用的領(lǐng)域還有很多,比如動力和能耗仿真、底盤操控仿真等等。不過因為篇幅的原因,我們就不一一介紹了。

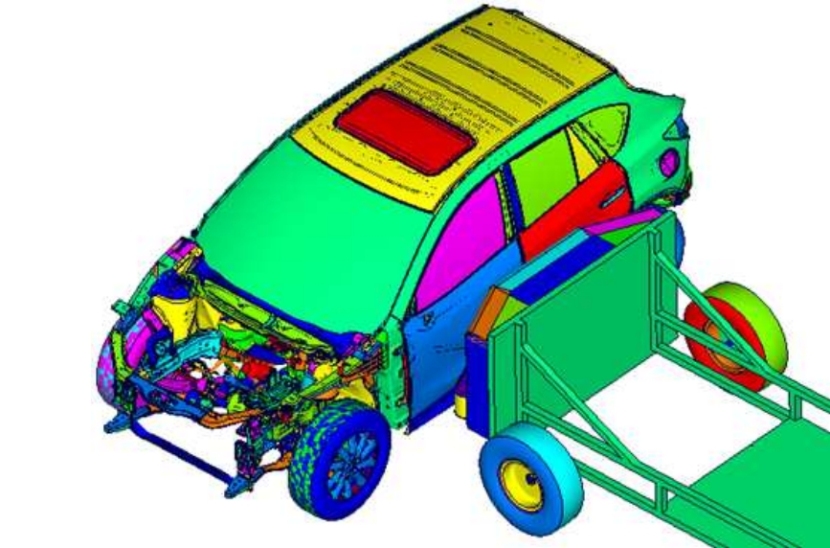
隨著CAE仿真技術(shù)的進步,新車在設計/驗證中大幅降低了試錯成本和研發(fā)周期。因為CAE在開發(fā)中特別好用,所以有不少廠商開始深度定制CAE軟件,并實現(xiàn)了自動化仿真。簡單來說,原本通用CAE軟件需要人工手動操作,流程比較繁瑣,而且還會出現(xiàn)人為的誤操作。而自動化仿真將部分或全部的手動操作變成了自動操作,進一步提高了效率,并降低了人為誤操作的概率。也就是說,即便各大車企都采用CAE仿真,他們之間的效率也會因為軟件性能或者算力的差異,影響整車的開發(fā)周期。


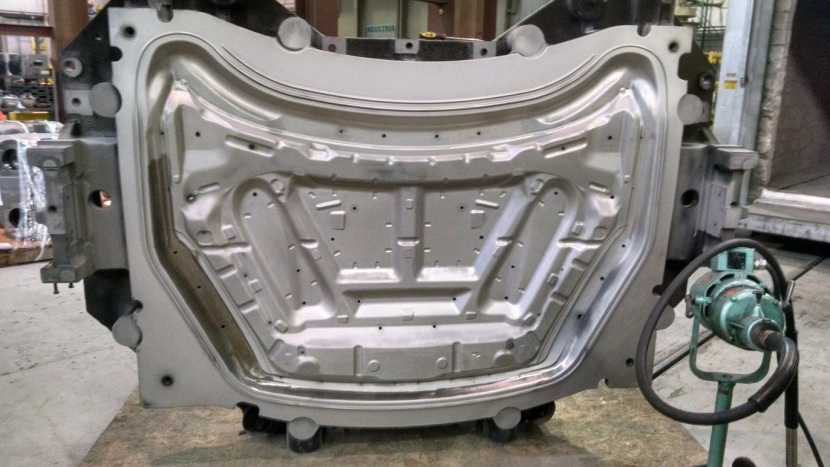
除了設計技術(shù)進步帶來的效率提升之外,部分汽車廠商為了進一步壓縮產(chǎn)品的研發(fā)時間和成本,的確對開發(fā)環(huán)節(jié)做了優(yōu)化。比如在傳統(tǒng)的汽車研發(fā)中,有一個開軟模試制樣車的環(huán)節(jié)。軟模的壽命很短,一般小于1000次,而大規(guī)模生產(chǎn)的硬模則可以達到20萬次。開軟模試制樣車主要是為了提前測試車身零部件的匹配和功能,如果車身存在設計缺陷,那么就可以提前發(fā)現(xiàn)問題,而不會把缺陷帶到開硬模的量產(chǎn)階段。
按照36個月的新車開發(fā)周期計算,軟模耗時為4個月,砍掉開軟模環(huán)節(jié)可以顯著縮減產(chǎn)品開發(fā)周期。有車企做過估算,要想把新車36個月的開發(fā)周期降到24個月,軟模是必須要省去的環(huán)節(jié)。之所以有車企敢省去軟模環(huán)節(jié),主要也是因為現(xiàn)在的CAE仿真的精度很高,開模的風險變小了。當然,在壓縮汽車開發(fā)環(huán)節(jié)過程中,類似的情況還有很多。


不僅是樣車試制,車輛耐久性和老化性能測試在如今的環(huán)境下也不得不進行縮減。比如有車企已經(jīng)使用了VPG技術(shù)部分替代了傳統(tǒng)的道路測試,簡單來說,VPG就是通過激光掃描典型的強化測試路面,然后建立一個路面的模型,把車輛和路面的模型同時導入到前面用來做碰撞測試的LS-DYNA軟件中,于是就可以通過軟件來測試車輛在強化路面上的耐久性能。
前面提過,大眾開發(fā)一款新車的時間為54個月,但是大眾目前正在研發(fā)的ID.2純電轎車開發(fā)周期已經(jīng)縮減至36個月。這其中仿真測試起了很大作用,原來大眾開發(fā)新車會在寒冷天氣做2-3個冬季道路測試,但是用到仿真測試后,現(xiàn)在只用做1個冬季測試。
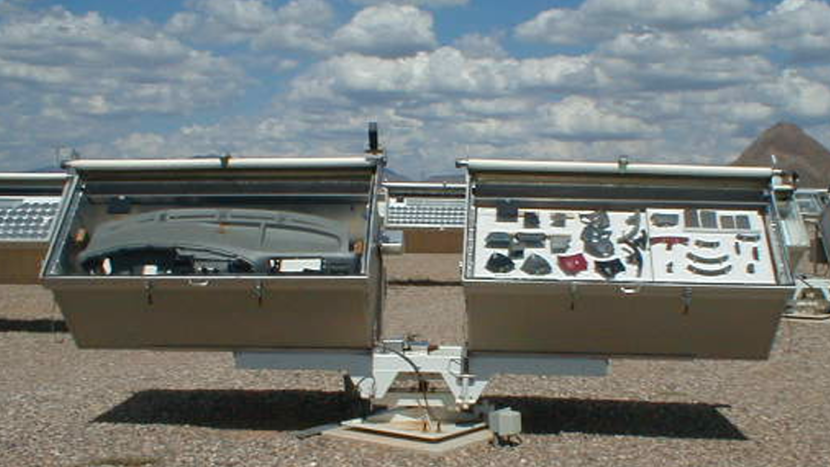
不過,耐久性仿真并不是全能的,像是車輛的實際磨損、腐蝕和老化依然不能通過仿真很好的體現(xiàn)出來。而傳統(tǒng)的戶外自然老化測試,一般又需要1年或者以上的時間,這顯然不符合現(xiàn)在的新車開發(fā)節(jié)奏。所以如今部分傳統(tǒng)的車企采用了相對保守的做法,那就是將零件、材料以一定溫度、濕度放在臺架上進行循環(huán)測試。至于臺架測試也無法有效驗證的零部件,則是單獨用樣件進行戶外測試。
但是不同企業(yè)的臺架老化測試標準差異還是很大的,就單單拿測試時間來說,有的企業(yè)臺架老化測試是120h,有的是1020h。

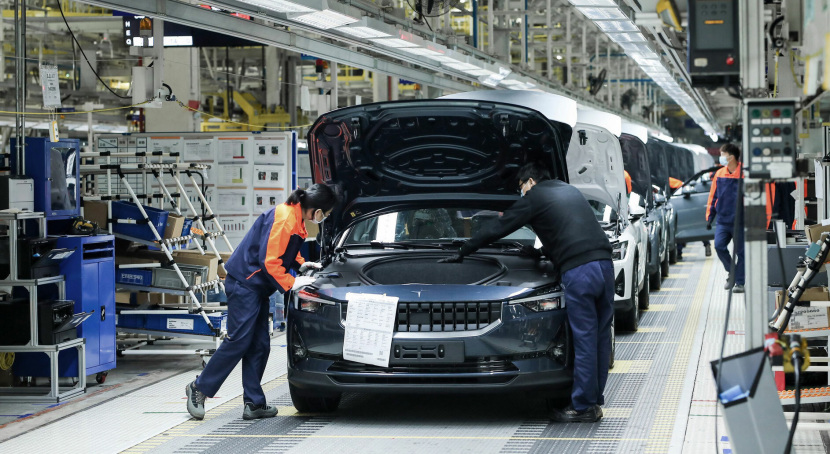
毋庸置疑的是,隨著造車技術(shù)的進步,新車的研發(fā)周期肯定會越來越短,而且車輛的品質(zhì)也能有所保證。但即使現(xiàn)在的仿真軟件可以一定程度上代替實際測試,這也不意味著新車的開發(fā)周期可以無限制地縮短。畢竟汽車不是手機,不會一兩年就更新?lián)Q代,而且使用的場景也要比電子產(chǎn)品復雜嚴苛許多。作為車企,應該本著為車主負責的態(tài)度,用合理的方式方法降本增效,而不是一味地壓縮新車開發(fā)測試的時間。